Plastic injection tooling is essential for the production of plastic parts and components. In a highly competitive market, it is crucial for manufacturers to produce high-quality plastic parts that meet their customers' demands in terms of performance, durability, and aesthetics. Molds are a critical component of the plastic injection process, and their quality directly impacts the quality of the final product.
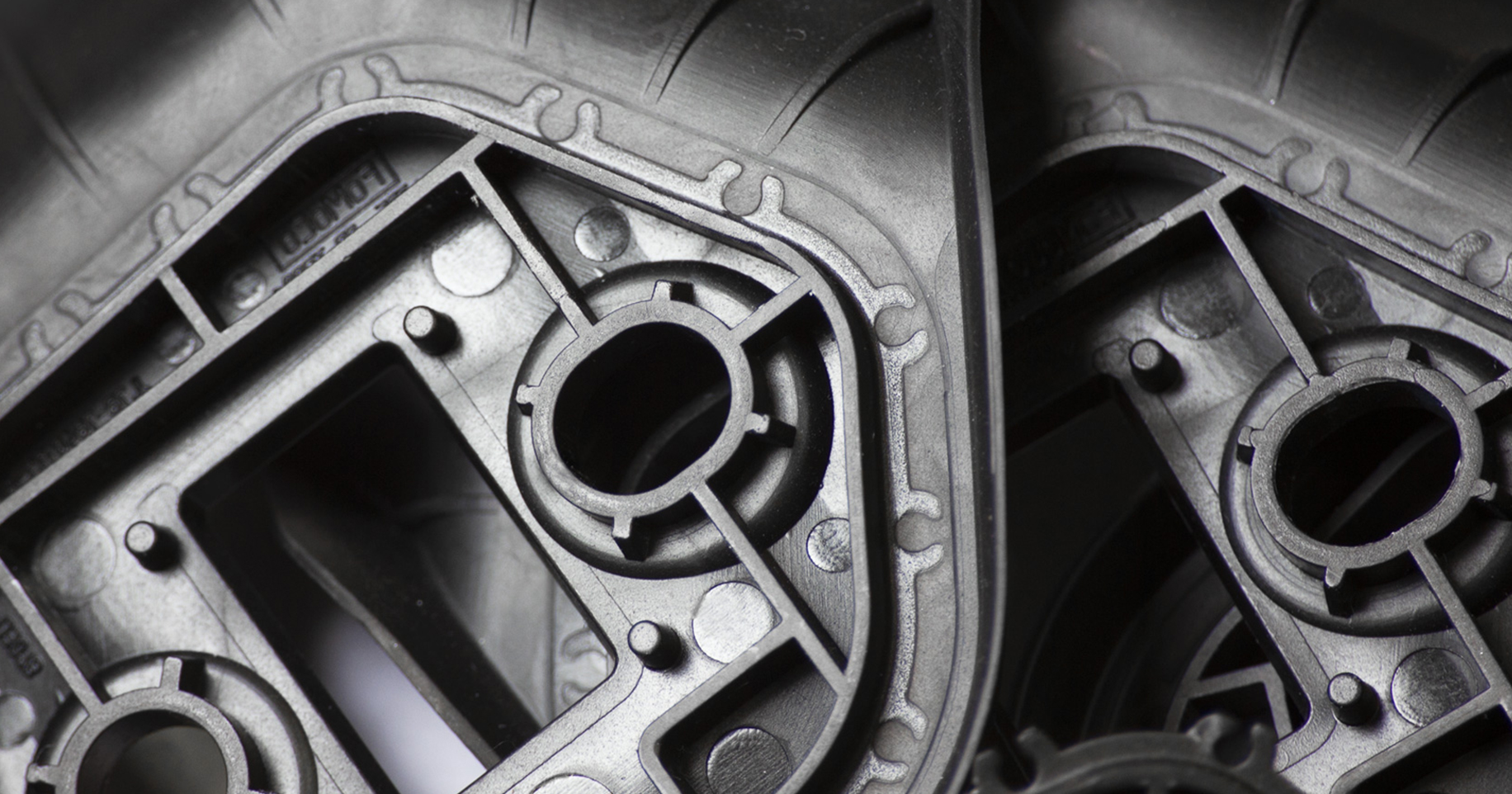
Molds are used to produce plastic parts in a process called injection molding. This process involves melting plastic pellets and injecting the molten plastic into a mold cavity. Once the plastic cools and hardens, the mold is opened, and the finished part is removed. The process can be repeated many times, producing uniform parts with high precision and consistency.
Molds come in different shapes and sizes and are made from various materials. The most common materials used for molds are steel and aluminum. Steel molds are more durable and can withstand high temperatures and pressures, making them suitable for high-volume production. Aluminum molds are lighter and less expensive, making them ideal for low-volume production. Molds can also be customized to meet specific design requirements, such as complex geometry and surface finishing.
High-quality molds are essential for producing high-quality plastic parts. Molds must be designed and constructed to meet the required tolerances, surface finishes, and dimensional accuracy. Any defects or imperfections in the mold can translate into defects in the final product, leading to product failures and warranty claims. Therefore, manufacturers should invest in high-quality molds to ensure the quality and consistency of their plastic parts.
In addition to molds, other components such as mold bases, ejector pins, nozzles, and mold cores contribute to the quality of the plastic injection process. These components must also be designed and constructed to meet the required specifications and tolerances. Mold bases provide the foundation for the mold and ensure accurate alignment and positioning of the mold components. Ejector pins are used to remove the finished parts from the mold, and they must be durable and capable of performing thousands of cycles. Nozzles are used to inject the molten plastic into the mold cavity, and they must be properly designed to prevent leaks and maintain consistent flow. Mold cores are used to form the internal features of the part, and they must be precise and durable.
Conformal cooling is a relatively new technology that is gaining popularity in the plastic injection industry. Conformal cooling involves designing cooling channels inside the mold that conform to the shape of the part being produced. This technology can significantly reduce cycle times, improve part quality, and reduce wastage. Conformal cooling can also reduce mold costs by reducing the amount of material required for the mold.
In conclusion, plastic injection tooling plays a critical role in producing high-quality plastic parts that meet customers' demands. Molds must be designed and constructed to meet the required tolerances, surface finishes, and dimensional accuracy. Manufacturers should invest in high-quality molds to ensure the quality and consistency of their plastic parts. Other components such as mold bases, ejector pins, nozzles, and mold cores also contribute to the quality of the plastic injection process. Conformal cooling is a new technology that can significantly improve the efficiency and effectiveness of the plastic injection process.