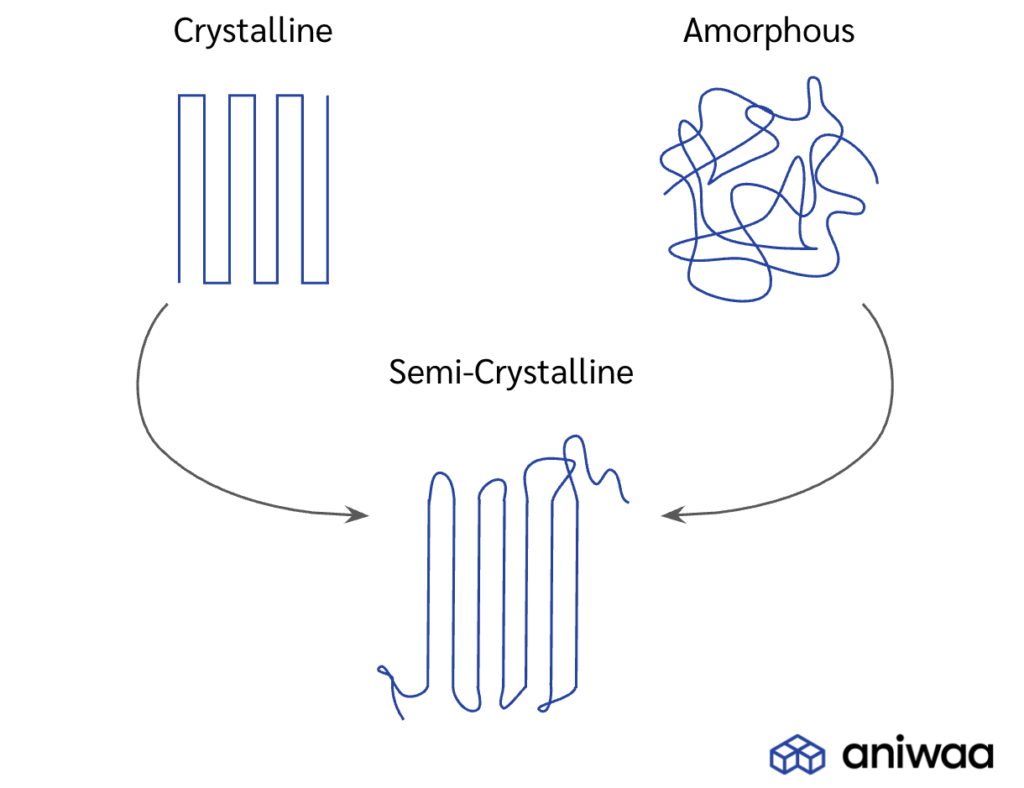
Injection Molding: Melting Amorphous vs. Semi-Crystalline Plastics
Plastics have transformed the way we live, work and play. From the plastic bags we use to carry our groceries to the intricate medical implants that help us live longer and healthier lives, plastics have revolutionized modern life. However, not all plastics are created equal. There are two main types of plastics: amorphous and semi-crystalline plastics. These two types of plastics have very different properties, and understanding the differences in how they melt is crucial to obtaining melt uniformity in injection molding.
At Shenzhen Zhongda Plastic Mould Co., Ltd., we have established ourselves as a one-stop solution manufacturer for all your plastic needs. Whether it is product design, mold design, mold making, injection molding, or assembly products, we have the expertise and experience to deliver high-quality products that meet your specific requirements. In this blog, we will discuss the differences between amorphous and semi-crystalline plastics and how to melt them to achieve melt uniformity in the injection molding process.
Amorphous Plastics
Amorphous plastics are plastics that do not possess a defined crystalline structure. These plastics have a disordered molecular structure, which makes them softer and more flexible than semi-crystalline plastics. Examples of amorphous plastics include polystyrene, acrylic, nylon, and polycarbonate.
When amorphous plastics are heated above their glass transition temperature (Tg), they become soft and rubbery. Glass transition is the temperature at which an amorphous plastic undergoes a transition from a glassy or brittle state to a rubbery state. Above Tg, the amorphous plastic can be easily molded into the desired shape. However, heating amorphous plastics too much can cause them to degrade or burn, which can result in poor melt uniformity during the injection molding process.
To melt amorphous plastics, the temperature must be carefully controlled. The temperature should be high enough to soften the plastic but not so high that it degrades or burns. It is important to use a high-quality screw with a low compression ratio in the injection molding machine to ensure uniform melt temperature and pressure.
Semi-Crystalline Plastics
Semi-crystalline plastics are plastics that possess a defined crystalline structure. These plastics have a more ordered molecular structure, which makes them harder and less flexible than amorphous plastics. Examples of semi-crystalline plastics include polyethylene, polypropylene, and acetal.
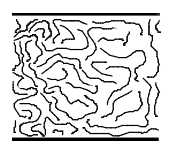
Semi-crystalline plastics have a melting point (Tm) at which they change from a solid to a liquid state. The melting point is the temperature at which the crystalline structure of the plastic begins to break down, and the plastic becomes a liquid. To achieve uniform melt temperature during the injection molding process, it is important to heat the plastic to just above the melting point and maintain the temperature within a narrow range.
A high-quality screw with a high compression ratio should be used to melt semi-crystalline plastics. The screw should have a deeper channel, which provides more surface area for heat transfer. Additionally, the screw should have a longer compression length, which allows the plastic to be heated more evenly.
Conclusion
At Shenzhen Zhongda Plastic Mould Co., Ltd., we understand the importance of melt uniformity in the injection molding process. By carefully controlling the temperature, pressure, and screw design, we can achieve uniform melt temperature and pressure, which results in high-quality products that meet our customers' specific requirements. Whether you need product design, mold design, mold making, injection molding, or assembly products, we have the expertise and experience to deliver the results you need. Please contact us to discuss how we can help you with your next plastic project.